800 Tons/day Large Pig Feed and Concentrated Pellet Production Line Project
Date: 11/23/2020 08:42:10 From: feed-pellet-plant.com Clicks:
This article mainly introduces the pig feed pellet production line and the concentrated feed pellet production line process and the required equipment list. It also includes investment costs, floor space, consumption of raw and auxiliary materials, etc. Richi Machinery provides factory construction guidance for customers who want to invest in pig feed pellet production projects or concentrated pellet production projects in the early stage.
800 Tons/day Large Pig Feed and Concentrated Pellet Production Line Project
1. Project Construction Content and Construction Scale
The designed production scale of this project: an annual production of 240,000 tons of feed (20 thousand tons of concentrated feed, 100,000 tons of suckling pig feed, 120,000 tons of fat pig feed), that is, 800 tons/day large pig feed and concentrated pellet production line. There are two 40-60 T/H feed pellet production lines, and two SLZH858 feed pellet machine from Richi Machinery are used. The planned land area of the project is about 55,687.38 square meters, and the total project investment is about 98 million yuan. The main construction content of the project includes: comprehensive building, workshop, warehouse, boiler room and supporting works of the site, public works, etc.
Pig Feed Pellet
The plant of this project can be divided into three parts: production area, supporting facility area and office area according to process layout requirements. The production area is located in the middle of the land and on the north side of the land. It is composed of production workshops, raw material warehouses, finished product warehouses, etc.; the office area is located on the west side of the base; the supporting facilities area is located at the east of the base, mainly consisting of a boiler room and auxiliary rooms. The layout of the entire land is compact and regular, which meets the national requirements for the layout of industrial land. The project composition and project content are shown in Table 1, and the main technical and economic indicators of the project are shown in Table 2.
Table 1 Project composition and project content
Project classification | project name | Construction Content | Remarks | |
structural work | Raw material library | 2 buildings with a total of 16560m 2 | ||
workshop | 2 buildings with a total of 3800m 2 | |||
Finished product library | 2 buildings with a total of 16560m 2 | |||
Research Building | 2 buildings with a total of 10150m 2 | 5F | ||
Auxiliary engineering | Comprehensive Building | 1 building with 2F, 866.32m 2 | ||
dormitory | 1 building with 2F, 980m 2 | |||
Boiler Room | 180.00 m 2 | |||
Coal shed | 216.00 m 2 | |||
Auxiliary room | 3816.84 m 2 | |||
Silo | 3816.84 m 2 | |||
Public works | Water supply | Park water supply network | ||
powered by | Park power supply network, power distribution room 288 m 2 | |||
Environmental Engineering | Greening | Green area 8342m 2 | ||
Exhaust | Boiler: wet desulfurization (calcium method) + bag dust removal + 40m chimney process dust: air collecting hood + pulse bag filter + 15m exhaust tube Fume: oil fume purifier + exhaust pipe |
|||
Sewage treatment facility | Septic tank, canteen grease trap | |||
RCPs | The southwest corner of the plant, covering an area of 50m 2 |
Table 2 Table of main technical and economic indicators
Serial number | project name | unit | Engineering Amount | Remarks |
1 | Total area | m 2 | 55,687.38 | |
2 | Total surface area | m 2 | 56284.00 | |
among them | 1#Raw material library | m 2 | 8280.00 | |
2#Raw material library | m 2 | 8280.00 | ||
3#Workshop | m 2 | 1900.00 | ||
4#Workshop | m 2 | 1900.00 | ||
5#Finished product library | m 2 | 8280.00 | ||
6#Finished product library | m 2 | 8280.00 | ||
1#Research Building | m 2 | 5075.00 | 5F | |
2#Research Building | m 2 | 5075.00 | 5F | |
Comprehensive Building | m 2 | 866.32 | 2F | |
dormitory | m 2 | 980.20 | 2F | |
Boiler Room | m 2 | 180.00 | ||
Coal shed | m 2 | 216.00 | ||
Auxiliary room | m 2 | 384.00 | ||
Silo | m 2 | 3816.84 | ||
Power distribution room | m 2 | 288.00 | ||
Guard room | m 2 | 59.64 | ||
3 | Building density | / | 47.58% | |
4 | Volume rate | 1.01 | ||
5 | Greening rate | % | 14.98 | |
6 | parking space | A | 26 |
2. Raw and Auxiliary Materials
Table 3 List of raw and auxiliary materials consumption
Serial number | name | unit | Annual consumption | Remarks |
1 | corn | t | 118540 | Solid, no odor, non-toxic |
2 | Soybean meal | t | 77210 | Solid, no odor, non-toxic |
3 | Peruvian Fish Meal | t | 10670 | Powder, no odor, no toxicity |
4 | wheat | t | 10670 | Powder, no odor, no toxicity |
5 | 65% lysine | t | 1810 | |
6 | Dicalcium Phosphate | t | 3070 | |
7 | coal | t | 2572 | Zixing Local |
8 | Electricity | Wando | 480 |
3. Description of Feed Production Process
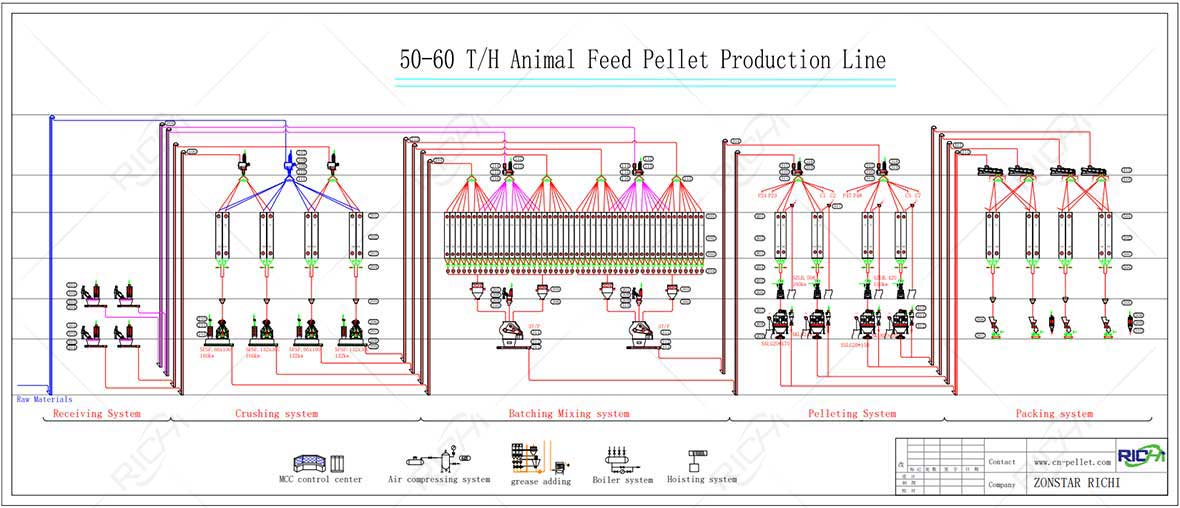
Flow chart of 50-60T/H feed pellet production line
(1) Raw material receiving system
Shredded material: Pour the material to be crushed into the pit, transport it to the elevator through the scraper conveyor, lift it to the cylinder for preliminary cleaning and sieve, then enter the permanent magnet cylinder to oscillate, enter the distributor and be distributed to the silo to be crushed. To be crushed.
Feeding of auxiliary materials without crushing: transported by a scraper conveyor to a hoist, and then lifted to a cylindrical powder sieve, then enters the permanent magnet cylinder to oscillate, and then transported by a scraper conveyor to the distributor to be distributed to ingredients Warehouse, to be mixed ingredients.
(2) Crushing system
The material to be crushed is in the silo to be crushed, and enters the crusher through the feeder for crushing, and then the crushed material is transported to the elevator through the screw conveyor, and then is lifted to the distributor, and then enters the batching silo to be mixed.
(3) Batching mixing system
The batching in the batching bin is passed through an automatic batching scale to make the raw material mixing ratio to a fixed value, and a certain amount of grease is added at the same time. Then the raw materials enter the mixer for mixing, and then enter the smashing bin through the scraper conveyor for two After pulverization, it passes through the elevator to the finished product inspection sieve. After sieving, the particles that meet the particle size requirements enter the permanent magnet cylinder for oscillation, and then pass through the distributor to the granulation bin.
(4) Feed pelleting system
After the raw materials are crushed, they are granulated by a pellet machine in the granulation bin, and then enter the crusher for crushing after being cooled by a cooler, and then pass through the elevator to the grading screen. The particles that meet the requirements enter the finished product bin through the distributor. This process mainly produces equipment noise.
(5) Ultrafine powder system
The particles that do not meet the requirements are batched through secondary mixing, enter the distributor through the batching scale, and then enter the micro-pulverizer.
(6) Puffing system
After being finely pulverized, the raw material enters the warehouse to be puffed, and is puffed by the puffing machine. After being dried by the dryer, it is transported to the grading sieve by the elevator, and the particles passing through the sieve enter the finished product warehouse.
(7) Packaging system
The finished product is firstly packaged by a scale, then sealed with a sewing machine, and finally transported to the finished product warehouse by a belt conveyor.
4. Main Production Equipment
Table 4 List of main equipment
Serial number | Equipment name | Specification model | Quantity (set batch) | |
The main production equipment | station | set | ||
Raw material receiving and cleaning system | 2 | |||
1 | Scraper conveyor | TGSS25 | 1 | |
2 | Bucket elevator | TDTGk50/28 | 3 | |
3 | Permanent magnet cylinder | TCXT25 | 3 | |
4 | Initial cleaning of drums | SCY80A | 1 | |
5 | Cone powder sieve | SCQZ80X90X110A | 1 | |
Crushing system | 2 | |||
1 | To be crushed | 3 | ||
2 | SFSP crusher | 968-V | 2 | |
3 | Crushing system wind net | 2 | ||
4 | High pressure fan | 6-30-8C | 2 | |
5 | Shakron | Φ1200 | 2 | |
6 | Wind shut | TGFZ16 | 2 | |
7 | Material sealing screw conveyor | TLSSF32 | 2 | |
8 | Bucket elevator | TDTGk50/28 | 2 | |
9 | Distributor | TFPX6-200 | 2 | |
Raw material expansion system (03) | 2 | |||
1 | Puffing warehouse | 2 | ||
2 | Feeding auger | TWLL16 | 2 | |
3 | Double jacketed conditioner | MUTZ420 | 2 | |
4 | Extruder | PHY260 | 2 | |
5 | Counter-flow flap cooler | SLNF24X24A | 1 | |
6 | High pressure fan | 6-30-8C | 1 | |
7 | High pressure fan | 6-30-5.5A | 1 | |
8 | Shakron | Φ1200 | 1 | |
9 | Shakron | Φ1000 | 1 | |
10 | Wind shut | TGFZ16 | 2 | |
11 | Material sealing screw conveyor | TLSSF25 | 1 | |
12 | Bucket elevator | TDTG50/28 | 1 | |
13 | Distributor | TFPX4-200 | 1 | |
Batching mixing system | 2 | |||
1 | Small material adding machine | SBLMa4 | 1 | |
2 | Pneumatic gate | TZMQ50X50 | 1 | |
3 | Small material adding machine | SBLMa4 | 1 | |
4 | Double shaft paddle mixer | SLHSJ7.0A | 1 | |
5 | Scraper conveyor | TGSS32 | 1 | |
6 | Permanent magnet cylinder | TCXT30 | 1 | |
7 | Bucket elevator | TDTGk50/32 | 1 | |
8 | Distributor | TFPX6-250 | 1 | |
Granulation system | 2 | |||
To be granulated bin | 2 | |||
Double jacketed conditioner | MUTZ1200 | 2 | ||
Pellet machine | SLZH858 | 2 | ||
Bucket elevator | TDTGk50/28 | 2 | ||
Scraper conveyor | TGSS25 | 1 | ||
Rotary classification screen | SFJH153X2(C) | 2 | ||
Finished product packaging system | 2 | |||
1 | Finished product warehouse | 3 | ||
2 | Electronic packing scale | LCS-50-BZ | 3 | |
3 | Sewing machine belt conveyor | 3 | ||
Inspection and testing equipment | ||||
1 | Weighbridge | SCS/ZCS-100D truck scale | 1 | |
Environmental protection and fire fighting equipment | ||||
1 | Dust removal equipment | Large pulse dust collector | 1 | |
2 | Boiler desulfurization + dust removal equipment | Wet desulfurization (calcium method) + bag dust removal | 1 | |
3 | Fire Equipment | Fire Fighting System | 1 | |
Other auxiliary equipment | ||||
1 | Grease adding machine | SYTC150 | 1 | |
2 | Air compressor | 3 cubic | 1 | |
3 | transformer | 1000KVA | 2 | |
4 | Boiler equipment | 15 ton coal-fired boiler | 1 |
5. Heating
This project uses a 15t/h steam boiler for heating, and the chimney height is 40m.
6. Labor quota and work system
The project plans to employ 200 people, including 35 managers. There are 165 marketing, production and other personnel. There are board and lodging in the factory, and about 100 people eat and lod in the factory. The project works 8 hours a day, 300 days a year.
The above is the article for you: 800 Tons/day Large Pig Feed and Concentrated Pellet Production Line Project. If you are interested in our products or project solutions, please contact us. We will give you the best product quality and the best price. Email: enquiry@pellet-richi.com
Related Product
Production Line Equipment
related News
- >Uzbekistan Nukus Chicken and Fish Feed Joint Pellet Production Lin
- >The Best-selling Commercial Automatic Pet Food Pellet Production L
- >Uzbekistan 10-15 TPH Chicken Mud Feed and Pellet Production Line W
- >Processing Project of Large-scale Feed Pellet Production Line With
- >Research Finds That Pellet Feed Can Improve Pig Feed Conversion Ef
- >600,000 Tons of High-grade Pig Feed Pellet Production Line Project
- >80 Tons/hour Large-scale High-end Pig Feed Pellet Production Line
- >Requirements for each section of the feed pellet production line
- >2020 China Feed Industry New Feed Pellet Production Line Project
- >What Are the New Feed Pellet Production Line Projects in 2019 (Par
Here you can submit any questions and we will get back to you as soon as possible. We will not disclose the information you submit to anyone, please rest assured.
Copyright© 2022 Richi Machinery. All rights reserved. Site Map