Processing Project of Large-scale Feed Pellet Production Line With an Annual Output of 240,000 Tons
Date: 01/07/2021 08:36:36 From: feed-pellet-plant.com Clicks:
If we talk about the high-yield feed pellet production and processing project in the feed industry, we have to mention the large-scale feed pellet production and processing project with an annual output of 240,000 tons in Guizhou Province.
Processing Project of Large-scale Feed Pellet Production Line With an Annual Output of 240,000 Tons
1. Project Overview of Large-scale Feed Pellet Production Line With an Annual Output of 240,000 Tons
(1) Project name: Feed processing project with an annual output of 240,000 tons in Guizhou Province;
(2) Construction nature: new construction;
(3) Construction site: Huaihua Industrial Park, Guizhou Province;
(4) Hourly output: 60 tons/hour pig, cattle and sheep feed pellet production line
(5) Daily output: 480 tons/day pig beef and sheep feed pellet production line, 480 tons/day pig beef and sheep meal feed production line
(6) Project investment: The total investment is 80 million RMB.
2. Construction Content and Scale of Large-scale Feed Pellet Production Line With an Annual Output of 240,000 Tons
The project will build a new feed processing plant and two production lines. After completion and put into production, the production scale can reach an annual output of 240,000 tons of pig feed, working 250 days a year. The project covers an area of 32,362 square meters and a total construction area of 24,462 square meters. The main construction contents are: new production workshops of 20,782 square meters, office buildings of 1,620 square meters, living rooms of 2,160 square meters, and other supporting buildings of 513 square meters. There are 35 parking spaces on the ground. The area and quantity of each building (structure) are shown in Table 1-1.
Table 1-1 List of details of structures (buildings)
Serial number | Building (structure) name | Building area (㎡) | Remarks |
1 | Production workshop | 20782 | |
2 | Office building | 1620 | |
3 | Living room | 2160 | |
4 | Power distribution room and maintenance workshop | 513 | |
5 | parking space | 35 | |
6 | Greening | 1600 |
The construction content of the project is shown in Table 1-2, and the main equipment of the project is shown in Table 1-3.
Table 1-2 List of construction contents
Engineering category |
Engineering Content | Project construction content | Remarks | ||
Main project | Feed mill | Main workshop and complete set of feed processing equipment | A total of 6 floors, with a construction area of 4200㎡ | ||
Finished product workshop | Building area of 1450㎡ | ||||
Raw material workshop | Building area of 7480㎡ | ||||
Auxiliary engineering |
dormitory | 1 building with 3 floors, with a building area of 1620 square meters | |||
administration building | 1 building with 4 floors, with a construction area of 2,160 square meters | ||||
Invoicing room, guard room | 1 building with 1 floor, covering an area of 513 square meters | ||||
Boiler Room | 1 building with 1 floor, covering an area of 450 square meters | ||||
other | Covers an area of 324 square meters | ||||
Public works |
Water supply | Supplied by the municipal water supply network in the park | |||
powered by | Supplied by the municipal grid, with a 1000KVA transformer | ||||
domestic sewage | Domestic sewage is treated in septic tanks and then discharged into the park sewage treatment plant for treatment | ||||
Boiler drainage | Drain into the rainwater pipe network after precipitation | ||||
Environmental Engineering | Waste gas treatment | Production waste gas | The raw material receiving, feeding, and crushing dust is collected and processed by the dust removal facility, and the uncollected dust is drawn out of the workshop by the fan for discharge. | ||
Canteen lampblack | 1 set of electrostatic fume purifier | ||||
Domestic sewage, canteen wastewater, laboratory wastewater | Septic tank | ||||
Floor washing wastewater, initial rainwater, boiler room wastewater | Reuse after sedimentation in sedimentation tank | ||||
Noise control | Choose low-noise equipment, through sound insulation, vibration reduction, and noise reduction | ||||
Solid waste treatment | Construct a temporary storage room for general solid waste (8m³). | ||||
The domestic garbage is cleared and transported by the sanitation department | |||||
Set up 1 hazardous waste temporary storage room with a scale of not less than 8m³ | |||||
Greening | 1600m³ |
Table 1-3 List of main equipment
Serial number | Equipment name | model | Quantity | Power (KW) | Remarks | |
1. The initial clearing section of raw material receiving | ||||||
1 | Scraper conveyor | TGSS25 | 1 | 3 | ||
2 | Bucket elevator | TDTG50/28 | 1 | 7.5 | ||
3 | Cylindrical cleaning screen | TCQY100A | 1 | 0.55 | ||
4 | Cone powder sieve | SCQZ90X80X110A | 1 | 11 | ||
5 | Pulse dust collector | TBLMb4 | 3 | 0.55 | ||
6 | Pulse dust collector | LNGm³0 | 2 | 5.5 | ||
2. Crushing section | ||||||
7 | Color Sorter | 1 | ||||
8 | Bucket elevator | TDTG40/28 | 1 | |||
9 | Impeller feeder | TWLY20×125 | 1 | 1.5 | ||
10 | "Beyond" Micro Pulverizer | SWFP66×125D | 1 | 200 | ||
11 | Fool grading screen | SFJH140X2B | 1 | 4 | ||
12 | Impeller feeder | TWLY20×100 | 1 | 1.5 | ||
13 | "Beyond" Micro Pulverizer | SWFP66×100D | 1 | 160 | ||
14 | silencer | 2 | ||||
15 | Pulse dust collector | TBLMy8 | 1 | 0.75 | ||
16 | Pulse dust collector | TBLMy108 | 2 | 30 | ||
17 | Pulse dust collector | TBLMb4 | 2 | 0.55 | ||
Three, livestock and poultry feed ingredients, mixing section | ||||||
18 | Ingredients cone | 3000KG | 2 | |||
19 | Fixed dust removal feeding screen | TLTSG100 | 2 | 0.49 | ||
20 | Ingredients cone | 2000KG | 2 | |||
twenty one | Fixed dust removal feeding screen | TLTSG100 | 2 | 0.49 | ||
twenty two | Scraper conveyor | TGSS32 | 2 | 5.5 | ||
twenty three | Bucket elevator | TDTG50/32 | 2 | 7.5 | ||
twenty four | Finished product inspection screen | SCQZ55X46X150 | 2 | 18.5 | ||
(1): Granulation section | ||||||
25 | Conditioner | MUTZ1200X2/MUTZ600X2JCJ | 2 | twenty two | ||
26 | Pellet machine | SZLH768 | 2 | 200 | ||
27 | Countercurrent cooler | SKLN28X28B/SKLN24×24B | 2 | 7 | ||
28 | Centrifugal fan | TLGF-LY-55/TLGF-LY-37 | 2 | 93 | ||
29 | silencer | 2 | ||||
30 | Fool grading screen | SFJH180×2C | 2 | 5.5 | ||
31 | Ingredients cone | 150KG | 2 | |||
(2): Finished product packaging section | ||||||
32 | Packing scale | LCS-50 | 2 | 2.2 | ||
33 | Seam combined conveyor | 2 | 1.1 | |||
34 | Pulse dust collector | TBLMy15 | 1 | 5 | ||
(3): Expansion pre-mixing system | ||||||
35 | Pulse dust collector | TBLMb4 | 1 | 0.75 | ||
36 | Ingredients cone | 1000KG | 1 | |||
37 | Double shaft mixer | SLHSJ2A | 1 | 18.5 | ||
(4): Raw material expansion section | ||||||
38 | Conditioner (double layer) | MDTZ260X2 | 1 | 15 | ||
39 | Livestock and poultry feed extruder (cooker)-corn, barley, etc. | SXPS260 | 1 | 200 | ||
40 | Raw material turning plate countercurrent cooler | SLNF24×24 | 1 | |||
41 | Centrifugal fan | Gm³7C | 1 | 37 | ||
42 | silencer | 1 | ||||
43 | Hammer Mill | SWFP66x80 | 1 | 90 | ||
44 | Pulse dust collector | TBLMy76 | 1 | 30 | ||
45 | silencer | 1 | ||||
(5): Auxiliary section | ||||||
46 | Oil storage tank | 2 | ||||
47 | Air compressor | 2 | 37 | |||
(6): Thermal production and supply | ||||||
48 | Gas boiler | 4t/h | 1 |
3. Raw and auxiliary materials of Large-scale Feed Pellet Production Line With an Annual Output of 240,000 Tons
The raw materials required for production during the operation period of this project are mainly: corn, rice bran, bran, soybean meal, rapeseed meal, biological fermentation raw materials and premixes, etc. Accessories such as salt and additives, and packaging materials are woven bags. Boiler fuel natural gas: 750,000 cubic meters per year, working 250 days a year.
The consumption of main raw materials and auxiliary materials is shown in Table 1-5.
Table 1-5 List of raw and auxiliary materials consumption
Serial number | name | Consumption T/a | Remarks (source and storage method) |
1 | corn | 144000 | Outsourcing, silo |
2 | Soybean meal | 36000 | Outsourcing, silo |
3 | Cotton meal | 13875 | Outsourcing, raw material warehouse |
4 | Rapeseed meal | 4050 | Outsourcing, raw material warehouse |
5 | Puffed soybeans | 2475 | Outsourcing, raw material warehouse |
6 | Fish meal | 1800 | Outsourcing, raw material warehouse |
7 | Expanded corn | 5625 | Outsourcing, raw material warehouse |
8 | Dicalcium Phosphate | 2700 | Outsourcing, raw material warehouse |
9 | Stone powder | 2250 | Outsourcing, raw material warehouse |
10 | Lysine | 2475 | Outsourcing, raw material warehouse |
11 | salt | 2925 | Outsourcing, raw material warehouse |
12 | Whey powder | 2475 | Outsourcing, raw material warehouse |
13 | Soy Lecithin | 1575 | Outsourcing, raw material warehouse |
14 | flour | 3600 | Outsourcing, raw material warehouse |
15 | Secondary fan | 2925 | Outsourcing, raw material warehouse |
16 | Peanut bran | 3150 | Outsourcing, raw material warehouse |
17 | Rice bran | 2025 | Outsourcing, raw material warehouse |
18 | Feed premix | 3825 | Outsourcing, raw material warehouse |
19 | Other additives | 2250 | Outsourcing, raw material warehouse |
total | 240000 |
4. Product plan of Large-scale Feed Pellet Production Line With an Annual Output of 240,000 Tons
The feed product plan produced by this project is shown in Table 1-7.
Table 1-7 Feed product plan
Serial number | project | Output (ten thousand t/a) |
1 | Powdered compound feed | 12 |
2 | Pellet feed | 12 |
5. Labor quota and work system of Large-scale Feed Pellet Production Line With an Annual Output of 240,000 Tons
(1) Construction period
The construction period of this project is expected to be 12 months. The labor force during the construction period is 10 people. One shift system is implemented. Each shift works 8 hours during the day and no construction at night.
(2) Operation period
During the operation period of this project, the labor force is 35 people, and the one-shift system is implemented. Each shift works 8 hours during the day and does not produce at night. The annual operating days is 250 days. The project has a dormitory and a canteen, and all employees eat and stay in the factory.
6. Process flow of Large-scale Feed Pellet Production Line With an Annual Output of 240,000 Tons
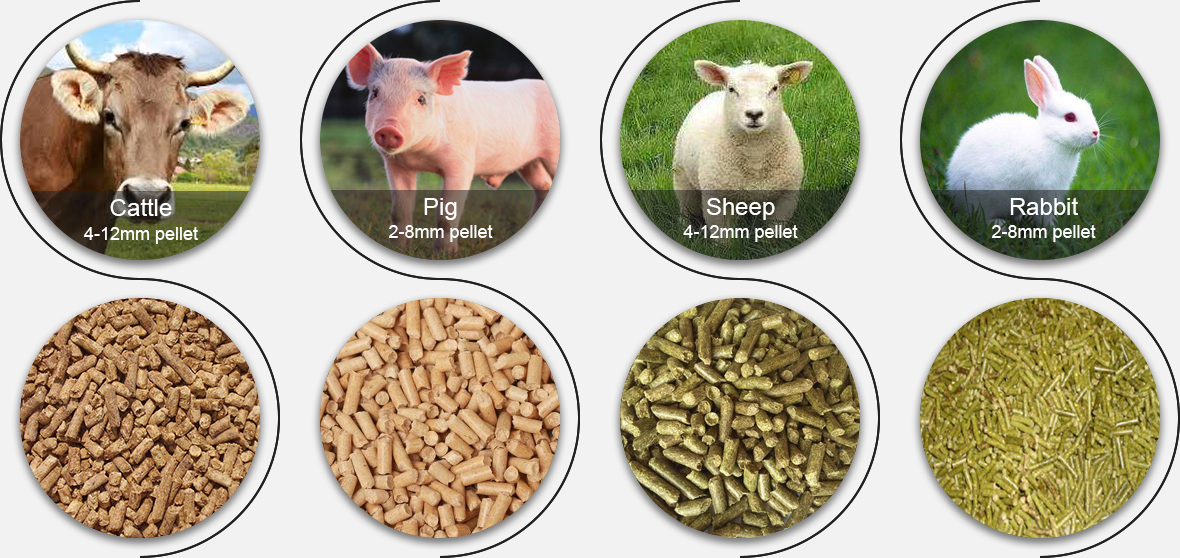
Pigs, cattle, sheep and feed pellets
(1) Picking and feeding: After the raw materials are purchased, they are unloaded to the raw material warehouse for storage;
(2) Preliminary cleaning and magnetic separation: The received feed materials contain a small amount of impurities, so the raw materials should be cleaned. The material enters the cylinder primary cleaning screen and the permanent magnet cylinder through the screw conveyor and the elevator. After removing large impurities and iron impurities, enter the vertical silo;
(3) Crushing: The crusher is mainly used to crush corn, sorghum and soybean meal. The cleaned materials enter the pulverizer for pulverization, and then are conveyed by the screw conveyor, respectively enter the elevator, and are introduced into the batching bin through the distributor;
(4) The protein powder, cotton meal, and premix are introduced into the batching bin through the distributor by the elevator;
(5) Ingredients: The system is equipped with an ingredient warehouse and an ingredient scale to ensure that the ratio is strictly implemented according to the formula;
(6) Mixing: mix the measured raw materials, auxiliary materials, feed additives and mixed oil;
(7) Conditioning: After the materials are mixed, steam conditioning is added, and the materials before granulation are hydrothermally modulated, so that the materials can fully absorb heat, moisture and liquid, so that they can meet and approach the requirements of the granulation process;
(8) Granulation: the granulation section is to enter the quenched and tempered mixture into the feed pellet mill for granulation of various specifications;
(9) Cooling: adjust the air volume according to the granulating speed to meet the cooling requirements;
(10) Crushing: After the material is cooled, it enters the crusher for crushing.
(11) Screening: The feed is screened by the screening machine, and the unqualified products are returned to the crushing section for crushing, and the products that meet the requirements of the standard enter the finished product warehouse by the elevator;
(12) Measuring and packaging: qualified feed products are packaged and packaged according to requirements by a packing scale, and then stored in the warehouse.
The above is the article for you: Processing Project of Large-scale Feed Pellet Production Line With an Annual Output of 240,000 Tons. If you are interested in our products or project solutions, please contact us. We will give you the best product quality and the best price. Email: enquiry@pellet-richi.com
Related Product
Production Line Equipment
related News
- >Analysis of Cost, Income and Economic Benefits of Large-scale Shee
- >Large-scale Commercial Feed Factory Cattle Cow Feed Pellet Machine
- >Investment Analysis of 5000 Tons/year Forage Grass Feed Pellet Pro
- >50,000 Tons/year Caragana Pellet Cattle and Sheep Feed Production
- >How Much Does It Cost to Invest in a Pellet Processing Plant With
- >Uzbekistan 10 t/h Large-scale Poultry Pellet Feed Processing Proje
- >12.5 Tons/hour Extruded Single Feed Raw Material Powder Production
- >Production and Processing Project of 300,000 Tons of Powdered Catt
- >Animal Feed Processing Production Line Project With an Annual Outp
- >1000 Tons/Day Large-scale Cattle Sheep and Chicken Feed Pellet Mil
Here you can submit any questions and we will get back to you as soon as possible. We will not disclose the information you submit to anyone, please rest assured.
Copyright© 2022 Richi Machinery. All rights reserved. Site Map