Cattle Feed Pellet Machine--machinery Equipment Specially Made for Cattle Feed Pellet
Date: 06/03/2020 11:31:35 From: feed-pellet-plant.com Clicks:
Cattle feed pellet machine, a kind of mechanical equipment specially made for cattle feed pellets. There are two types of cattle feed pelletizers on the market: flat die pelletizers and ring die pelletizers. Flat die pelletizers have low output, low investment, and quick results. Generally, the tonnage is below 1t/h. The tonnage of the ring die pellet machine is above 1t/h, with large investment and large output, suitable for large-scale farms and cattle feed pellet suppliers.
Cattle Feed Pellet Machine
Raw material of cattle feed making machine
1. Cereals: maize, barley, oat, wheat, triticale, rye and sorghum
2. Seed from oleaginous crops: soy, flax, and sunflower
3. Seed from legumes: broad beans, field bean and protein pea
4. Forage: flours of permitted forage essences
5. Dried beet pulp.
Furthermore, the following substances can be used as appetizers in feed pellets:
1. Carob-bean, up to a maximum of 3%;
2. Molasses, up to a maximum of 3%.
Note: for animals in lactation, dry animals, and heifers from the sixth month of pregnancy, maximum daily amount of feed pellets is 2 kg/head/day.
cattle feed
Production process of cattle feed pellet machine
The major operations involved in the production of cattle feed pellets are: raw materials preparation, primary crushing, molasses mixing, fine crushing, pellet making and packaging(optional)
★ Raw and auxiliary materials are first charged into silos and tanks where they are made ready for further processing. They are then processed by primary crusher. Crushed materials are further separated by means of a sieve, and then stored in the assorting tanks according to the kind of raw materials.
★ The raw materials are then mixed by means of a feed mixer. In this process, fatty ingredients are added to the materials in order to raise the nutritional value of the feed. The feed obtained from the mixer is blended with molasses.
★ Assorted animal feed that is crushed into fine particles is further formed into pellets by a cattle feed pellet mill.
Factors affecting pellet quality of cattle feed
Several factors have an effect on the quality of the pellets. First of all the feed formulation (raw materials and additives used). Some feed ingredients have a good impact on pellet quality, while others could adversely affect the quality. Unfortunately, corn-soy diets are not the ideal diets to achieve the desired pellet quality. Dietary inclusion of wheat grain or wheat by products (wheat midds, wheat gluten) can increase pellet durability, because of the high protein (gluten) and hemi-cellulose content of wheat in comparison to corn or corn co-products. Similarly inclusion of oat as a partial substitute of corn can increase pellet quality.
We can rank feed grains according to their positive impacts on pellet quality from best to worst as followings:
- oat,
- wheat,
- barley,
- corn,
- sorghum.
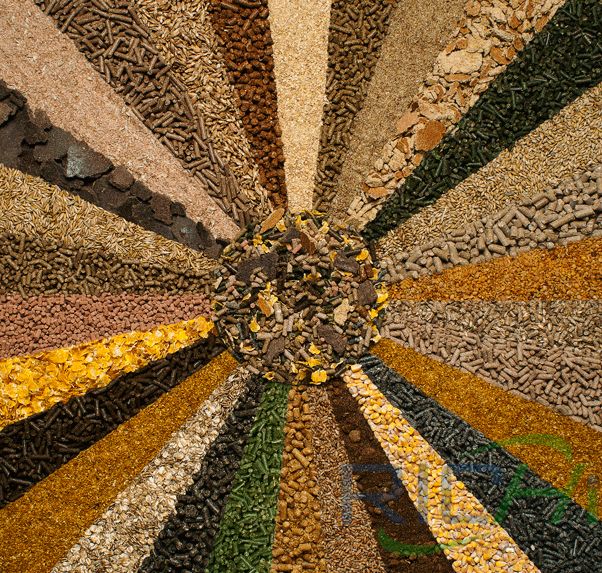
Raw material of cattle feed making machine
1. Affect of steam on pellet quality
Processing obviously has a large effect on pellet quality as well. When mash feed passes through the conditioner, it is exposed to high pressure steam. This steam provides the heat and moisture required for starch gelatinisation, particles adhesion, feed semi-digestion, and feed pathogens damage. The steam temperature and the time that mash feed stays in the conditioner have major influence on the durability of the produced pellets. Conditioning the feed at a temperature of 80° C is sufficient to produce good quality pellets. The minimum time that feed should stay in the conditioning tube to produce durable pellets is 30 seconds. Long time conditioners, in which the feed can stay in the conditioner for about 3-4 minutes, can be used to improve pellet stickiness.
2. Thicker dies have positive impact on pellet durability
Also die/roll specifications should be kept in mind. Pellets are produced via roll pressing of the hot mash against metal die. Thicker dies (long die channels) have a positive impact on pellet durability due to increasing the friction time between feed particles and die wall with subsequent more starch gelatinisation. Most of starch gelatinisation occurs when feed passes through the dies. A similar result can be obtained by using small hole dies. This means that dies of 60 mm thickness are better than those of 50 or 40 mm thickness, and that dies with holes of 3 mm diameter are better than those with holes of 5 mm diameter. However, using thicker or small holes dies have negative impact on pellet throughput. Additionally, increasing the distance between roll and die from 0.1 to 2 mm resulted in an increase in the pellet durability.
3. Affect of ingredient particle size and grinding on pellet quality
The second factor influencing pellet quality is the feed ingredient particle size. Although doubted by some researchers, it is accepted that decreasing ingredient particle size has a good influence on pellet quality. However, over grinding is not recommended to avoid power wastage, reduced production rate and suboptimal gizzard development. On the other hand, coarse grinding eases pellet break down and decreases starch gelatinisation (high degree of gelatinisation is required to produce good pellets).
4. The cooler should be taken into consideration.
After leaving the pellet mill, the temperature of the pellets ranges from 70-90° C and the moisture from 15-17%. Proper cooling (via a stream air cooling machine) is required to lower pellet temperature to about 8° C above the ambient temperature, and moisture % to be 12%. The cooling machine can be either a horizontal or vertical type. Quick cooling leads to removal of more moisture and heat from the surface of the pellets than their core, and the resultant pellets will be brittle. On the other hand, prolonged cooling produces very dry pellets that can be exposed to abrasion and can be of low palatability.
Figure 1 - Factors affecting pellet quality
Pellet quality can be influenced by several factors, including the ingredients, diet formulation and processing. A good rule of thumb is the pellet quality factor (PQF), that each feed ingredient has. The PQF has a score from 0 to 10, where 0 predicts poor pellet quality and 10 good pellet quality. From experience we know that starch and its gelatinisation is the most important factor for achieving the desired pellet quality. However, recent reports indicated that the positive impact of protein on pellet quality is much more important than that of starch.
Related Case
3-4T/H Ruminant Animal Feed Pellet Line Export To Hong Kong,China
3-5T/H Ruminant Animal Feed Pellet Line Export To Indonesia
5-6T/H Cattle Feed+10T/H Chicken Feed Pellet Production Line Export To Saudi Arabia
10T/H Ruminant Feed Pellet Line Export To South Africa
The above is the article for you: Cattle Feed Pellet Machine--machinery Equipment Specially Made for Cattle Feed Pellet. If you are interested in our products or project solutions, please contact us. We will give you the best product quality and the best price. Email: enquiry@pellet-richi.com
Related Product
Production Line Equipment
related News
- >Delivery 200kg/h Floating Fish Feed Production Machine Line to Mol
- >Uzbekistan 5t/h Aquatic Sinking Fish Feed Production Machine Line
- >Uzbekistan 3-5 T/h Medium Scale Automatic Poultry Feed Line Manufa
- >Uzbekistan Nukus Chicken and Fish Feed Joint Pellet Production Lin
- >Uzbekistan Gizak 1t/h-2t/h Animal Feed Processing Plant for Floati
- >Afghanistan 10t/h animal feed pellet line
- >What is the price of the cattle and chicken feed machinery product
- >Can You Send Me an Animal Feed Pellet Machine Quotation?
- >The Best-selling Commercial Automatic Pet Food Pellet Production L
- >How to Choose Premix for Cattle Feed Manufacturers?
Here you can submit any questions and we will get back to you as soon as possible. We will not disclose the information you submit to anyone, please rest assured.
Copyright© 2022 Richi Machinery. All rights reserved. Site Map