Post-thermal Application of Feed Additives in Feed Pellet Production Line
Date: 10/12/2020 09:00:43 From: feed-pellet-plant.com Clicks:
Feed Pellet Mill
Introducing an alternative design of feed processing line to protect heat-sensitive materials
Compound feed is a mixture of main ingredients, including grains, protein supplements and by-products, and feed additives (micro-ingredients) such as minerals, vitamins, commercial enzymes, probiotics and prebiotics.
In conventional feed mills, these 2 categories of ingredients are placed in a mixer to produce a uniform mixed feed. Then this feed is transported to the conditioner where the feed is subjected to thermal processing and continues on, passing through a hot die to produce hot pellets. In the next step, the temperature and moisture of pellets are reduced by a cooler. For a typical design of such a feed pellet production line see Figure 1. In this kind of feed pellet production line both main ingredients and feed additives are cooked.
Figure 1 – Conventional design for feed processing line.
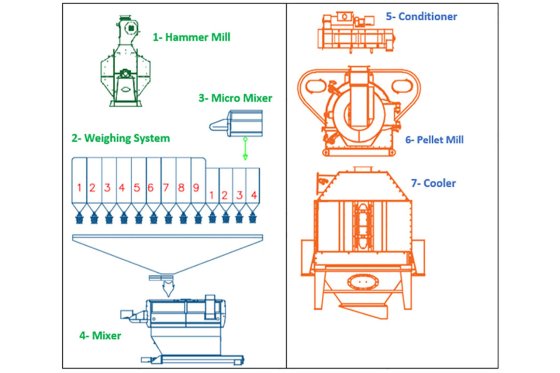
Avoid detrimental effects on feed ingredients
However, thermal processing is a double-edged sword; the applied heat has both positive and negative effects on the main ingredients, but its effects on feed additives usually are negative. Many feed additives, especially commercial enzymes, probiotics and vitamins are expensive and sensitive to heat, thus it is suggested to protect them from the detrimental effects of thermal processing. the feed industry uses three solutions to maintain heat-susceptible materials:
Excess or over-use of materials to compensate for potential losses during the heating process. This means there is lavish use of expensive materials.
Using a heat-resistant or coated form for some materials to protect them from heat. In many cases, the protection is not complete and this is not possible for all materials.
Vacuum coating is a technological solution that can be applied to materials after thermal processing. This technology is usually applied to oils and liquids, and requires additional investment and energy. Nevertheless, it is viable for high-margin products such as extruded aqua feed and pet food.
Figure 2 Proposed new design for the feed pellet production line.
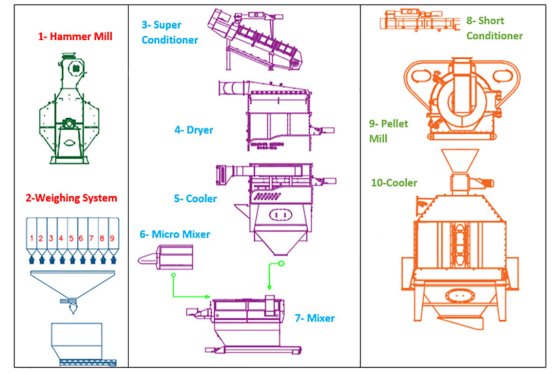
Alternative design feed pellet production line
Figure 2 introduces a novel design of the feed processing line. In this design, the main ingredients are grinded, weighed and then subjected to conditioning by a super conditioner. Since the feed additives are not yet added to the main ingredients, it is possible to use higher temperatures (e.g. >90 ˚C) and longer retention times in the super conditioner, for instance for hygienising purposes.
In the dryer and cooler, the conditioned main ingredients will lose the heat and moisture absorbed in the conditioner. After this stage, feed additives are mixed in a micro-mixer to produce a premixture which is added to the main ingredients in a mixer. Then the final mixture is subjected to mild conditioning with only 40-50 ˚C (by a small amount of steam or even hot water) before being pelleted by the pellet mill.
In spite of mild conditioning at this stage, the quality of the pellets (e.g. the pellet durability index and hardness) will remain satisfactory because of the previous conditioning. Practical results show that the energy consumption of pellet mills has decreased and the output of pellets (tonnes/h) and the longevity of the die have increased in this design. After the pelleting process is complete, the temperature and moisture of pellets are reduced by a cooler.
Design advantages and disadvantages
The suggested feed processing line has advantages and disadvantages compared with a conventional feed processing line.
Advantages:
Less thermal loss of feed additives
Flexibility to apply more thermal treatments (higher temperature and extended conditioning time) of the main ingredients without any concern about feed-additive losses
Flexibility to use low-value crops and by-products using appropriate thermal processing
Producing more hygienic feed using higher temperatures and retention time in the conditioner
Usable for dry (powder) forms of feed additives
Better mix uniformity of dry feed additives with the conditioned main ingredients
Disadvantages:
More initial investment is needed because of the need to add an additional mixer and dryer
More attention needs to be devoted to the hygienic quality of purchased feed additives (because there is less thermal application)
Conclusion
Feed additives such as vitamins, probiotics, and commercial enzymes are expensive components of modern animal feed. Most of these materials are heat-sensitive. To maintain the efficacy of these materials, the feed industry uses different strategies, including excess use of materials, a heat-resistant or coated form for some materials and vacuum coating technology. Nevertheless, these methods are expensive and have limitations.
An alternative method to protect feed additives is to install a mixer layout after thermal processing and to add feed additives to the mixer to avoid the high temperatures.
Related News
4* 30 Tons/hour Feed Pellet Mill Production Line Technical Solutions And Prices
Cost Price Of 1-2T/H, 5-8 T/H, 10-12 T/H and 15-30 T/H Feed Pellet Machine
Feed Pellet Machine Is Used For 900000 Chickens In Uganda
Mauritania 10T/H Animal Feed Pellet Production Line Project Case
The above is the article for you: Post-thermal Application of Feed Additives in Feed Pellet Production Line. If you are interested in our products or project solutions, please contact us. We will give you the best product quality and the best price. Email: enquiry@pellet-richi.com
Related Product
Production Line Equipment
related News
- >Delivery 200kg/h Floating Fish Feed Production Machine Line to Mol
- >Uzbekistan 5t/h Aquatic Sinking Fish Feed Production Machine Line
- >Uzbekistan 3-5 T/h Medium Scale Automatic Poultry Feed Line Manufa
- >Uzbekistan Nukus Chicken and Fish Feed Joint Pellet Production Lin
- >Uzbekistan Gizak 1t/h-2t/h Animal Feed Processing Plant for Floati
- >Afghanistan 10t/h animal feed pellet line
- >What is the price of the cattle and chicken feed machinery product
- >Can You Send Me an Animal Feed Pellet Machine Quotation?
- >How to Choose Premix for Cattle Feed Manufacturers?
- >Professional Commercial Feed Production Line With a Daily Output o
Here you can submit any questions and we will get back to you as soon as possible. We will not disclose the information you submit to anyone, please rest assured.
Copyright© 2022 Richi Machinery. All rights reserved. Site Map